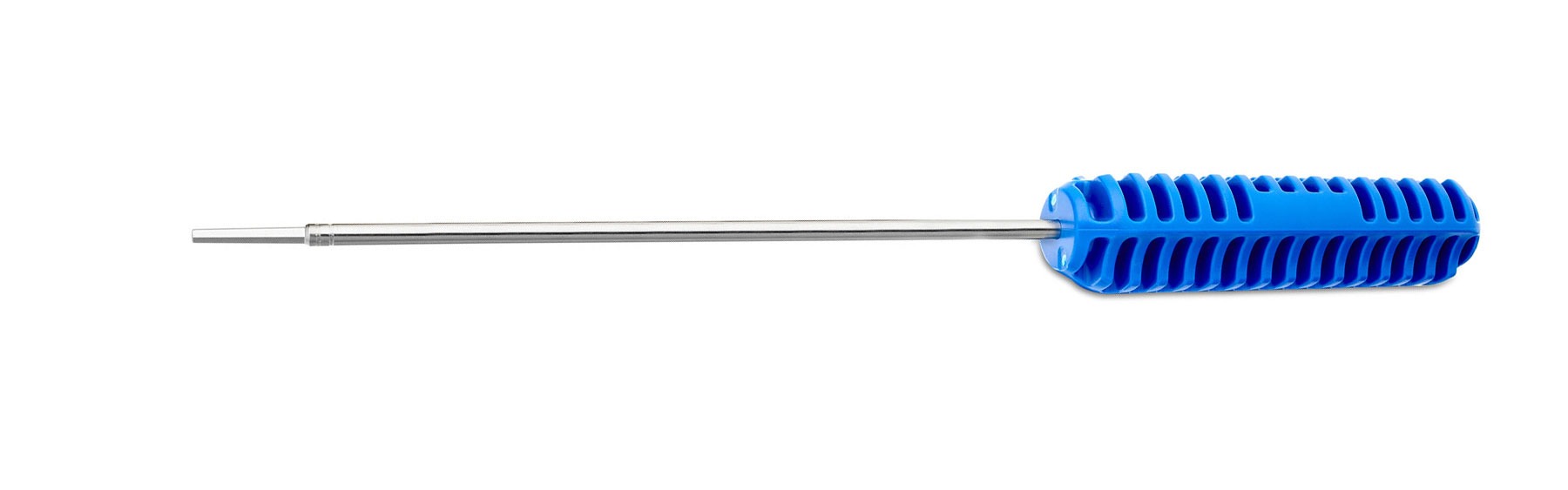
Insert Molding & Overmolding
Insert Molding
Insert molding involves placing a plastic or metal component (the “insert”) into the mold before injecting plastic around it. This process encapsulates or integrates the insert into the final molded part. It creates a strong component without the need for secondary assembly steps.
Insert molding highlights
- Plastic is molded around a pre-formed non-plastic component, often metal
- Allows plastic and metal (or another material) to be combined into one part with plastic encapsulating the metal
- The molded plastic can protect the inner part and then allows for sterilization
- Creates a strong part without need of assembly
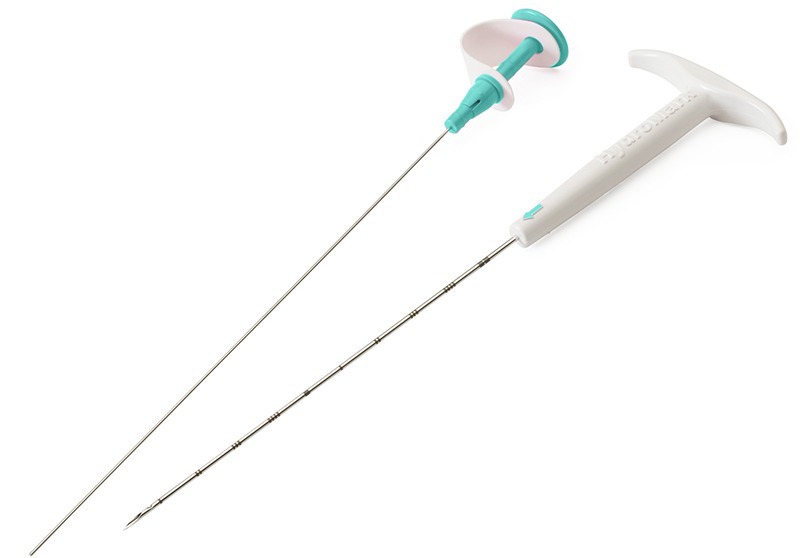

Examples of insert molding
- Handles molded onto the metal part of hand-held devices
- Hubs for drug delivery devices such as needles
- Hubs for oncology devices such as those used to collect biopsies
- Inhaler components
- Metering pump magnets
- Housings for pacemakers
- Housings for endoscopy devices
Overmolding
Overmolding allows us to apply multiple layers of materials onto a base component, enhancing device functionality, grip, and ergonomics. By over-molding plastics over metals or other plastics, we create custom, multi-material parts that offer comfort, durability, and improved functionality.
Overmolding highlights
- Enhanced ergonomics and usability of medical devices
- Creates strong bond between materials
- Supports a wide range of material combinations
- Enables intricate designs
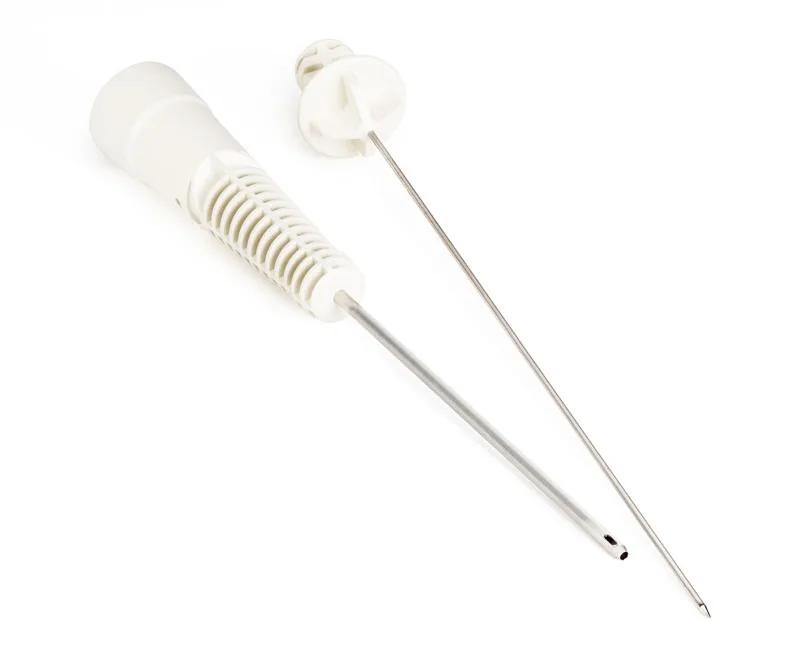

Examples of Use
- Ergonomic handles for precision medical devices
- Housings for diagnostic equipment like glucose monitors or ultrasound devices
- Insulin pens and auto-injectors with textured grips for ease of handling
- Pacemaker or defibrillator components with protective over-molded coatings
- Handles and grips for joint replacement and spinal surgery tools
- Wearable medical devices
Two-Shot Molding
Two-shot molding and insert molding are often confused, but each technology offers different benefits and applications for medical devices.
Two-shot molding, also known as 2K molding or double-shot molding combines two different thermoplastics into a single molded component. Two shot molding creates complex, multi-color, multi-material devices and components.
Two-shot molding highlights
- Combines two different thermoplastics into a single molded component
- Creates complex, multi-color, multi-material components
- Consolidates the number of parts
- Bonds are stronger than those from joining separate parts after molding
- Tighter tolerances
- Improved repeatability and accuracy
- Uses rotary table technology, index plate systems, and core-back technology as needed
- Expert, in-house mold building and decades of experience
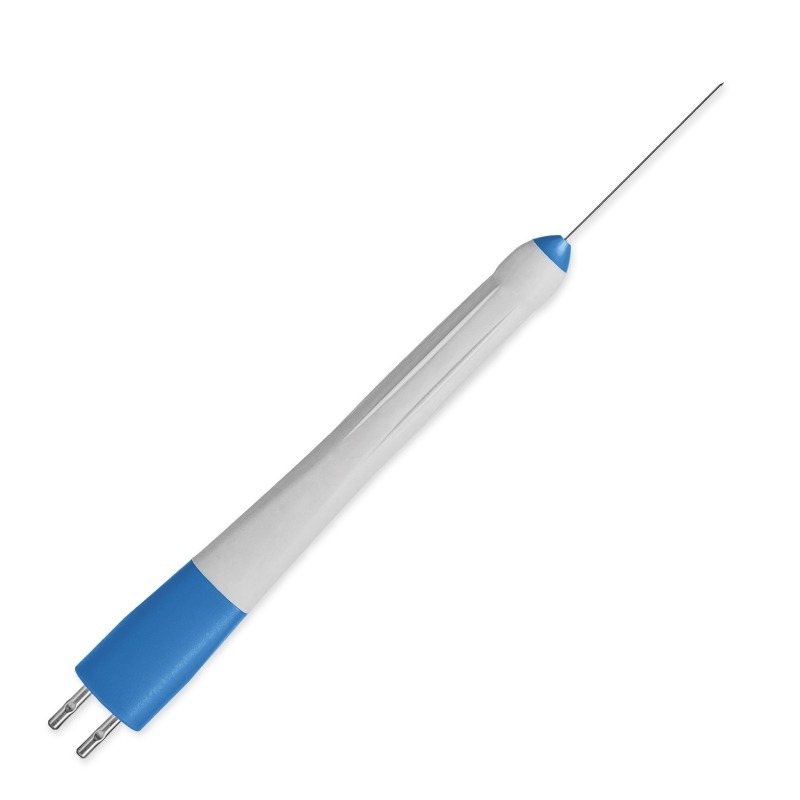
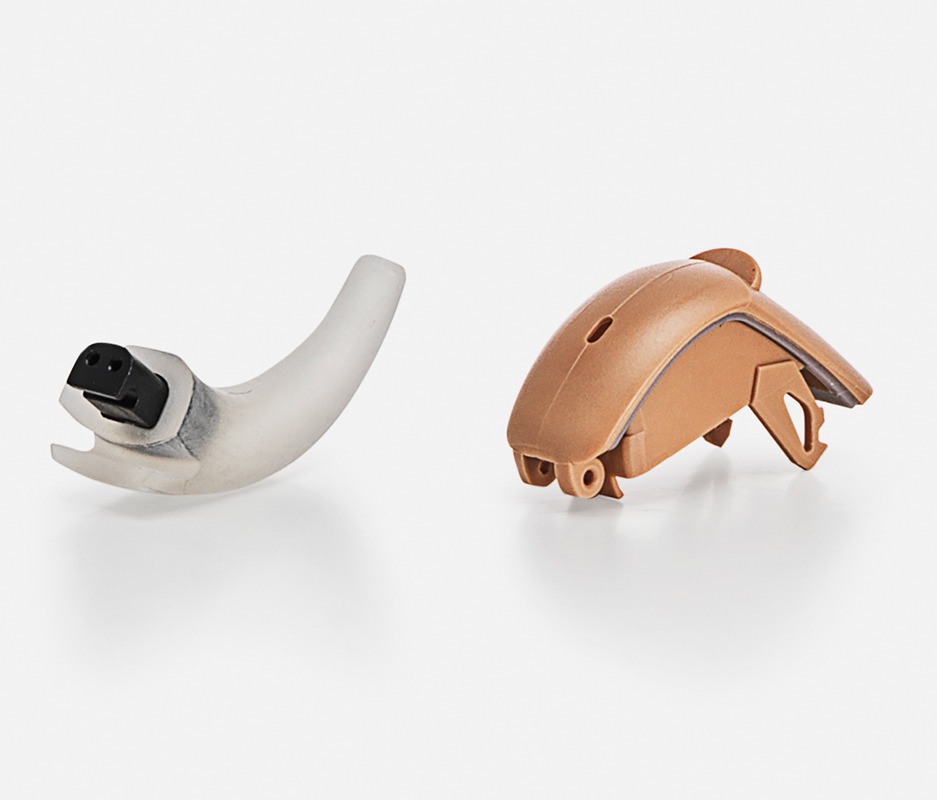
Examples of two-shot molding
- Instrument handles with a hard core and softer, ergonomic outer material
- Hearing aids
- Pacemakers and implantable cardioverter-defibrillators (ICD)
- Cardiovascular home monitoring devices
- Drug delivery devices
- Abutments for dental implants

Let’s Start the Conversation
Your next project begins with a conversation. Reach out to us today and let’s discuss your needs.